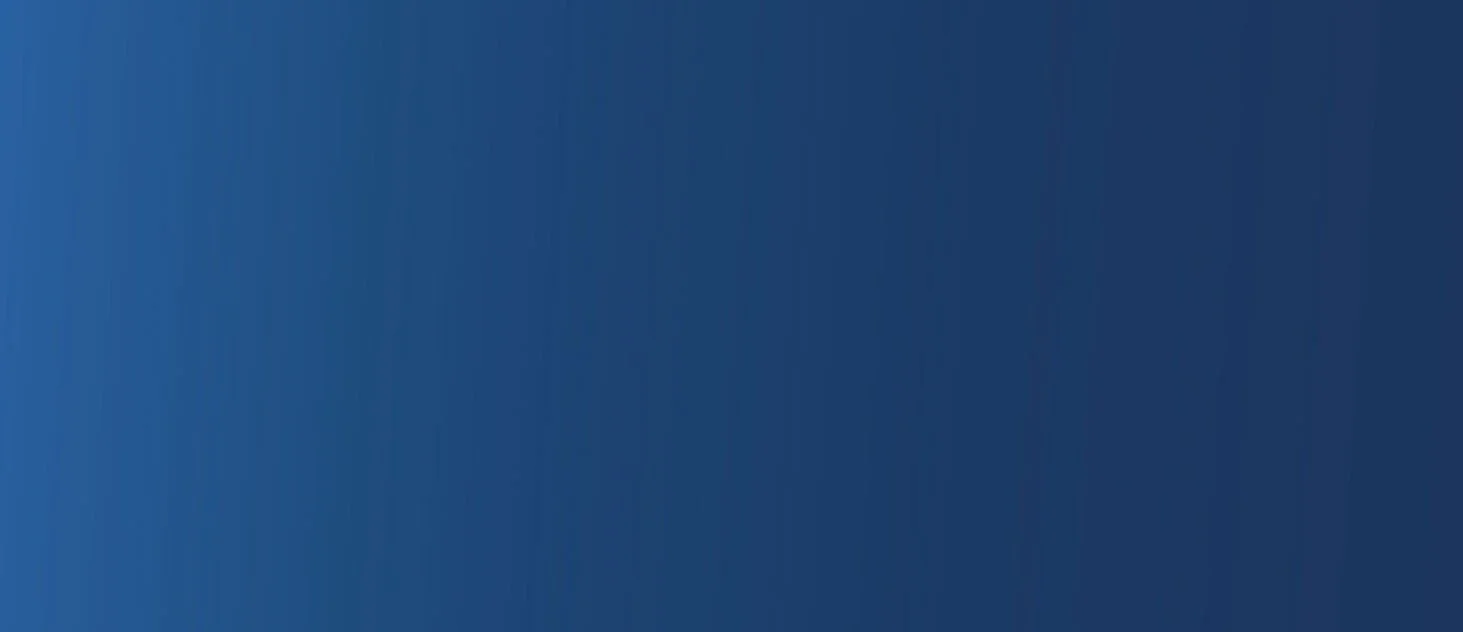
VFX
VFX AC DRIVES
For Constant Torque Applications
The Emotron VFX Variable Frequency Drive offers reliable, cost-effective, and user-friendly operation of constant torque applications such as crushers, mixers, mills, conveyors, and cranes, which require accurate and dynamic speed control.
User-friendly and Reliable Operation
Operation parameters can be set in your own process units - m/sec, tons/hour, cycles/min, etc. - making monitoring easier and more reliable. The removable control panel has a copy function for transferring settings to other Emotron VFX units. You can switch between local and remote control by the push of a button on the control panel. The built-in programmable logical functions, comparators and timers mean that, in many cases, external PLC or relays can be avoided.

KEY FEATURES
3 - 2,500 Amps
NEMA-rated enclosure (available in NEMA 1 and NEMA 12 configurations)
Unique Shaft Power Load Curve Monitoring and Protection
Internal Speed Controller
Integrated Vector Braking
Sleep function
Customizable process language feature, i.e., m/sec, tons/hr, cycles/min, etc.
Copy function via detachable display keypad
Smaller footprint than competing VFDs
Optimized for efficiency
-
Efficient starts and stops
Efficient and protective starts are ensured with Emotron VFX. Reduced start currents, thanks to direct torque control result in smaller fuses, cables, and energy bills. Torque can be boosted to overcome initial peak loads. Integrated vector braking ensures quick and controlled stops, increasing productivity and safety.
-
Optimized Operation and Full Control
The direct torque control reacts extremely quickly and eliminates disturbances due to abrupt load changes. A built-in load monitor and a unique Load Curve Protection function protect your process by immediately detecting any situation that could cause inefficiency or damage. Early warning and safety stops for over- and underloads allow preventative action.
-
Cost-Effective and Flexible Installation
The compact standalone 2.5 - 250A units are NEMA 12 (IP54) classified. The robust, all-metal construction can be installed close to the application, which eliminates the cost of additional cabinets and long motor cables.

Pulse width modulation (PWM)
In 1977, Emotron was the first company to introduce an AC Drive based on Pulse Width Modulation (PWM). Here we take a look at PWM and the impact it has had on today’s VFD technology.
-
In 1977, Emotron was the first company to introduce an AC Drive based on Pulse Width Modulation (PWM). Further developments led to one of the first market launches of AC Drives with Direct Torque Control in 1998. The Emotron technology has an extremely fast response time since actual and required torque is compared 40,000 times per second.
Emotron drives can provide the highest possible torque per Ampere from a normal industrial motor, offering the option of controlling a motor without a rotor sensor while still maintaining control of torque and speed.
-
First and foremost, the Direct Torque Control method, invented by Depenbrock and Takahashi, offers highly efficient control of dynamic and demanding applications. The Emotron technique reacts quickly to peak loads, abrupt load changes, or inaccurately set ramp times. The response time is compared 40,000 times per second. This is invaluable in crane control for example, where frequent and critical starts and stops demand instant high torque - or in crusher applications where speed quickly needs to be adjusted to the type or size of material.
-
With Direct Torque Control, the torque/current ratio is linear above nominal torque, i.e., 200% current results in 200% torque, compared to approximately 150% torque at 200% current without Direct Torque Control. Therefore, the overload capacity required for the Emotron AC Drive to stay in full control of the motor can be considerably lower than when using control methods without Direct Torque Control.
-
The Direct Torque Control works with the AC Drive’s integrated vector brake to ensure rapid and protective braking. The available braking torque is doubled compared to conventional braking methods. The braking energy is dissipated through the motor itself, which helps avoid interruptions due to excessive brake voltage. In most cases, no mechanical brakes are required. Brake choppers and brake resistors are needed only to achieve an extremely short braking time.
-
AC Drives with Direct Torque Control all operate with direct control of the motor’s torque and flux. This effectively eliminates false trips caused by shock loads, mains supply disturbances or inaccurately set ramp times. This is realized with a quick response and very accurate control of the motor flux based on the motor model used in the software. Each and every switching in the AC Drive is directly related to the electromagnetic state of the motor, resulting in smooth and accurate control at all times.
-
The essential part of the Direct Torque Control is the motor model which provides accurate estimates of the actual flux and torque of the motor.
By comparing the calculated actual values with reference values at an extremely high calculation frequency, a closed loop of flux and torque control can be achieved. All relevant motor parameters are measured automatically, the load inertia is checked and internal parameters are automatically set accordingly.
Together with superior braking capacity and precise control of acceleration and deceleration, this results in a torque response time that can be less than 1 ms and a speed accuracy as good as ±0.1% of rated rpm, even without a separate sensor on the motor. Typical values with conventional sensorless vector control are 50-100 ms torque response and ±1.2% speed accuracy.
VFX complete range NEMA 1 (IP20) and NEMA 12 (IP54) 690V portfolio: English
FDU/VFX IP20/21, Product brochure: English
FDU/VFX complete range - IP20/21 Sales Leaflet: English
FDU/VFX 2.0 Technical Catalog: English
FDU/VFX 2.1 Technical Catalog: English
VFX 2.0 High Power - Product brochure: English
VFX 2.0 Product brochure: English
Addendum FDU/VFX 2.1: English
Addendum Ferrite Core for FDU 48-090 and VFX 48-090: English
Addendum - Quick coupling for liquid cooled FDU/VFX 2.0 frame sizes E & F: English
FDU 2.0 Instruction manual: English
FDU 2.0 Quick setup guide: English
FDU 2.1 Instruction manual: English
Additional resources, such as drilling templates, quality and conformity documentation, communication options and more are available upon request.
Specifications (NEMA1 / IP20/21 version) | |
---|---|
Rated Power | 15 - 175HP (11 - 132kW) |
Supply Voltage | 3 x 230 - 480VAC |
Rated Current | 25 - 244 Amps |
Protection Class | NEMA 1 / IP20/21 |
Approvals | Global Standards |
Specifications (NEMA12 / IP54 version) | |
---|---|
Rated Power | 1 - 4,000HP (0.75 - 3,000kW) |
Supply Voltage | 3 x 230 - 690VAC |
Rated Current | 2.5 - 2,500 Amps |
Protection Class | NEMA 12 / IP54 |
Approvals | CE, UL, DNV, GOST R |
VFX IN YOUR INDUSTRY
Get in touch.
Want more information about our VFX Variable Frequency Drives? Please, drop us a line… we’re here to help!